Features & Specs
Solar Module Laminating & Inspection
Solar Panel Vacuum, Heating & Laminating Machine
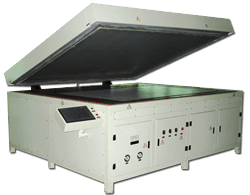
Semi-Automatic Solar Module Laminating & Pressing Machine
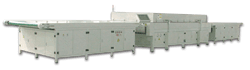
Fully Automatic Solar Module Laminating & Pressing Machine
Feature
- This machine is used to vacuum, heat, encapsulate, press, laminate and cure assembly solar module into an inseparable body. Solar cell could be mono crystalline or multi crystalline silicon.
- Assembly solar module is heated by hot oil resulting in uniform heating temperature.
- Compact design of vacuum chamber, heating plate and lower chamber.
- Vacuum cavity total sealed prevents air from leaking.
- Anti-wrinkle long life vacuum rubber lasts longer.
- Specially design reliable and maintenance free vacuum valve guarantees high vacuum degree.
- Noise depress high efficient vacuum pump minimizes vacuum time.
- Few pieces of solar module could be laminated within one batch.
- Semi-automatic and fully automatic machine are available. The heating, vacuum, pressing and laminating process of both machines is identical and is fully automatic. The only different is solar module loading and unloading.
- In semi-automatic machine, loading and unloading of solar modules are done manually. After loading, laminating cycle begins automatically.
- For fully automatic machine, there are inlet and outlet conveyors. There is also a belt conveyor in laminating machine. The conveyor belt is made of high temperature resistant fabric. Solar module is loaded on inlet conveyor. While inlet conveyor brings one batch of solar module into laminating machine, high temperature resistant belt conveyor brings preceding batch of solar module out onto outlet conveyor.
- Fully automatic machine fully utilizes the laminating machine while there is a lot of downtime in semi-automatic machine due to time consuming for solar module loading and unloading.
- In semi-automatic machine, top cover is tilted up and down by pneumatic cylinders. In fully automatic machine, top cover is supported by four columns which rises up or lowers down by means of hydraulic power.
Control
- Heating, vacuum, laminating and pressing processes are done automatically. In case of necessary, system can be switched to manual mode.
- Reliable PLC can be communicated with PC achieving industrial automation.
- User friendly HMI touch panel display simplifies parameters settings. Multi parameters are display in one window. Help files provides maintenance guide and trouble shooting.
- Parameters setting are safely save even though power is shut down.
- Three steps pressing control results in extremely high quality pressing and laminating performance. Pressing speed is adjustable. Top cover opening or closing speed is adjustable.
- Pressing cycle is count and record. Production capacity per shift are counted. This is also reference for maintenance and replacement of spare parts.
- The control system includes control of vacuum, pressure transmission, PID, programmable logic, relay, etc. This sophisticated system accomplishes complex requirement of mono-crystalline and multi-crystalline solar cell modules curing and encapsulation.
- There is pressure sensor which monitors vacuum status of vacuum chamber. Room atmospheric pressure can be re-set and adjusted according to altitude where machine is installed.
- Whenever power is shut down, top cover can be opened manually.
Safety Precaution
- After top cover is opened, cylinder is self-locked. Cover does not descend without further command.
- When there is any necessary, operator pushes emergency button. The machine will halt at its operating status.
- Whenever there is power cut off, emergency operation is activated to air fill and to open top cover.
- Tri-color indicating lamps provide real time operating status and signal alarms.
- Heated oil tank is equipped with observation window monitoring oil level. There is also an oil re-circulating pump and pressure indicator displaying pressure parameter. When there is insufficient oil, oil pressure drops and it harms oil re-circulation. Machine will alarm to refill oil preventing machine damaging from overheating.
- Oil temperature is dual controlled by over-temperature controller and module. This double safety design guarantees proper oil working temperature in case one of them is broken.
- Laminating temperature is controlled by PLC with PID.
- When oil and laminating temperature are above set values of super temperature controller and PLC, system alarms overheating signal and meanwhile, shuts down heating.
- After pressing and laminating are completed, lower chamber is air refill. Top cover stays lock and cannot be opened until lower chamber reaches atmosphere. If air refill is insufficient, system alarms and air refilling is continuous until it reaches atmosphere. In the meantime, system reminds operator to re-set re-filling duration to prevent insufficient air refill from occurring again.
- During laminating operation, there is alarm signal whenever vacuum pump is shut down. Vacuum pump shall generate requested vacuum degree and shall not stop during proper laminating process.
- System alarms if vacuum pressure cannot be reached in certain time. Command pops up in touch panel display asking “Continuous Vacuum” or “Air Refill & Open Top Cover”.
- System alarms if temperature measure is malfunction.
- When top cover lowers down and closes incompletely for subsequent operation, signal alarms. If upper chamber is started vacuum, it would damage upper rubber plate. If lower chamber is started vacuum, vacuum will never achieved due to unseal of upper and lower chambers.
- There is an alarm interface showing vacuum, oil level, over temperature, pressure when top cover open and motor status, etc. It helps maintenance and trouble shooting.
Specifications
Automation | Semi-Automatic | Fully Automatic |
Inlet / Outlet Conveyor | Nil | Yes |
Solar Module Loading/Unloading | Manually Load & Unload at Pressing Area | Manually Load on Inlet Conveyor & Unload on Outlet Conveyor |
Laminating Table Top | Fix | High Temperature Resistant Fabric Conveyor Belt |
Pressing Area | 1100 x 2200 mm | 2200 x 3600 mm |
Laminated Pressing & Curing Time | ~ 21 min. | ~ 21 min. |
Heating Method | SD340 Heat Oil Conduction | SD340 Heat Oil Conduction |
Hot Oil | L-QC-320 | L-QC-320 |
Temperature Control | PLC & Intelligent PID with HMI Touch Panel Display | PLC & Intelligent PID with HMI Touch Panel Display |
Temperature Range | 30 ~ 180 ℃ | 30 ~ 180 ℃ |
Temperature Control Accuracy | ≤±1.0℃ | ≤±1.0℃ |
Temperature Accuracy at Pressing Area | ±1.5℃ | ±1.5℃ |
Hydraulic Pressure | NA | 6 ~ 8 MPa |
Vacuum Pressure | 100 ~ 10 Pa | 100 ~ 10 Pa |
Vacuum Rate | 30 Lt/sec. | 30 Lt/sec. |
Compress Air Pressure | 0.6 ~ 1.0 MPa | NA |
Compress Air Consumption | 0.5 m3/min | NA |
Cooling Water Consumption | 2 Lt/min. | 2 Lt/min. |
Voltage | 380V / 3 Phase / 50Hz / 4 Wires | 380V / 3 Phase / 50Hz / 4 Wires |
Power | 27 KW | 77 KW |
Weight | 3.8 Tons | 17 Tons |
Outer Dimension(LxWxH) | 2560 x 1460 x 1270 mm | 13200 x 2800 x 1380 mm |
Trimming Table
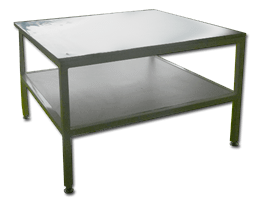
After laminating, solar modules are placed on this table. Operator trims, if there is any, surplus around solar module edges. It is a steel structure table. Table top is made of anti-static high density board.
Structure | Steel Structure with Anti-Static High Density Board Table Top |
Outer Dimension (LxWxH) | 1200 x 1220 x 760 mm |
Laminating Inspection Table
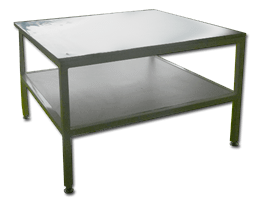
Solar module is put on this table for laminating properties checking and appearance inspection. It is a steel structure table. Table top is made of anti-static high density board.
Structure | Steel Structure with Anti-Static High Density Board Table Top |
Outer Dimension (LxWxH) | 1200 x 1220 x 760 mm |