Overview
MACHINE & COMPONENTS
High Pressure Pump
Reliable High Pressure Pumps Guarantees Consistent Pressurized Water at Lowest Running and Maintenance Costs
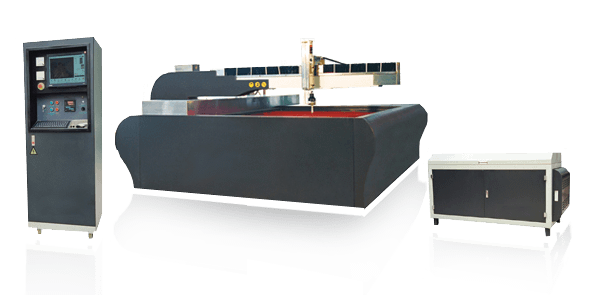
High pressure pump is the heart of water jet system. The pump pressurizes water and delivers it continuously through plumping and mixing tube until a supersonic waterjet stream exits out from jewel orifice. There are two types of pump used for waterjet application, direct drive based pumps and intensifier based pumps.
Direct Drive Based Pumps
This high pressure pump is similar to that used for house washing or deck prior to repainting. The triplex pump gets movement of the three plungers directly from the electric motor. For the moment, this type of pump delivers 138 MPa to 345 MPa (20,000 PSI to 50,000 PSI).
Due to its simplicity and cost competitive, direct drive based pump is widely used for general purpose applications.
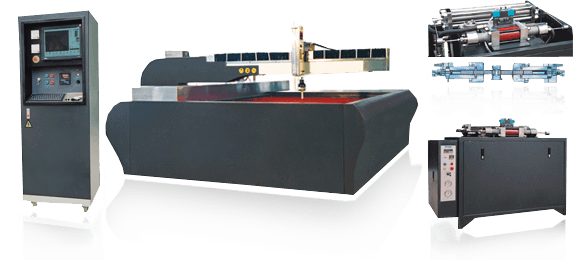
Intensifier Pumps
Ultra high water pressures are generated from intensifier based pumps. There are two fluid circuits running in a typical intensifier pump. They are water circuit and hydraulic fluid circuit. This pump is designed based on intensification principle which is, pressure is equal to force divided by area.
Water Circuit
General tap water runs, through a filter system, into the water circuit which is composed of booster pump, intensifier pump and shock attenuator. After filtering, the water enters into the booster pump with inlet water pressure maintained at approximately 0.7 MPa (100 PSI) ensuring the intensifier is always filled with water. After leaving from the boost pump, the water is delivered to the intensifier pump and is pressurized to 400 MPa (about 60,000 PSI).
The water then flows through the shock attenuator which is a large vessel used to dampen the pressure fluctuations created during sudden water pressurization at the intensifier pump. The back and forth action of intensifier piston creates pulsating flow of water at very high pressure. The shock attenuator cylinder acts as a high pressure surge vessel and is used to help the water flow more uniform resulting in smoother cut. This is to guarantee the water jet stream exiting the jewel orifice is steady and consistent. The water stream would visibly and audibly pulse and thus, marks would be left on material being cut if no shock attenuator is used.
Hydraulic Circuit
This circuit is composed of an electric motor, hydraulic pump, oil reservoir, manifold and piston biscuit and plunger.
The hydraulic pump is powered by the electric motor. Oil is hydraulically pumped from the reservoir and is then pressurized to 20 MPa (about 3,000 PSI). This pressurized oil is delivered to the manifold where manifold’s valves generate stroking action of the intensifier by pushing the oil to one side of the biscuit and plunger assembly, or the other. The intensifier pump consists of a double acting cylinder. It is a reciprocal such that the biscuit and plunger assembly reciprocates back and forth. By means of intensification principle, this action delivers high pressure water out from one side of the intensifier while low pressure water fills the other side.
In other words, hydraulic fluid is introduced alternately into one side and then another. The hydraulic piston alternately pressurizes the water using small diameter plungers at each end of the intensifier assembly. A series of check valves allows low pressure water into the plunger cylinder when the plunger retracts and then directs the pressurized water into the outlet manifold when the plunger moves into its compression stroke. The hydraulic fluid pushes on large piston to generate high force on smaller plunger. This plunger pressurizes water to a level that is proportional to the relative cross-sectional area of the larger piston and the small plunger.
If the cross-sectional area of the plunger is, say, 20 times smaller than the biscuit, the 20 MPa (about 3,000 PSI) of hydraulic pressure is intensified 20 times more resulting in 400 MPa (about 60,000 PSI) of water pressure. The intensification ratio is, in this assumption, 20 : 1. Higher intensification ratio will result in higher water pressure.
Plumbing
Special Stainless Steel Plumbing Delivers Steady Pressurized Water

The high pressure water is then transported to the water jet nozzle through high pressure plumbing. The plumbing is usually special stainless steel tube. The tubes are long enough providing freedom movement of the nozzle.
Different sizes of tubes are used for different applications.
Cutting Head
Precision and Sophisticated Cutting Head Allows Prefect Self-Alignment

Structure
The cutting head of abrasivejets is a two-stage design. It is mainly composed of jewel orifice, Venturi chamber and mixing tube.
Pressurized water flows through the jewel orifice forming a water jet stream. Abrasive particles are feed into the cutting head where they come across to the water stream inside Venturi chamber. Like a bullet in a rifle, the abrasive particles are accelerated down the mixing tube and are eventually exit out onto workpieces.
Jewel Orifice
It has a tiny opening. Pressurized water coming from the plumbing will flow into this orifice. This specially design and made orifice is used to convert the pressurized water into high velocity water stream.
Depending on different applications, orifice diameters are available from 0.2 mm to 0.35 mm. Orifice diameters out of the ranges are sometimes used for special applications.
There are three common types of orifice materials. They are sapphire, ruby and diamond. Each of the materials has its own unique attributes.
Sapphire - It is the most popular material widely used today. This artificial single crystal jewel generates fairly good quality water stream. For pure waterjet process with good water quality, it lasts between 100 to 200 hours depending on practical operations. The life time could be reduced to half for abrasive waterjet application.
Ruby - It is more preferable for abrasive waterjet rather than pure water jet. The stream generated is not suitable for pure water jet application. It has similar life time to sapphire.
Diamond - It runs from 800 - 2,000 operating hours but is 10 to 20 times more costly than sapphire and ruby. Unlike sapphire and ruby orifice, diamonds can sometimes be cleaned by ultrasonic and reused. Due to long life time and maintenance friendly, diamonds, among costly, are selected when 24 hours a day, 7 days a week operations are required.
Venturi Chamber
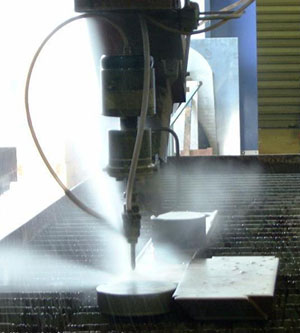
This chamber is where the abrasive meets the water.
After the water stream passes through the orifice, it travels downwards and enters into this small Venturi chamber at a very high velocity.
Meanwhile, abrasive is feed sideward into this chamber where Venturi effect creates a vacuum to pull abrasive and air downwards leaving the chamber.
Mixing Tube
When the abrasive and water leave the Venturi chamber, the water accelerates the abrasive and enters into a long and hollow cylindrical mixing tube where they are mix with each other. The mixture of abrasive and water form a coherent stream while exiting the mixing tube. This coherent stream gains enormous energy to perform cutting.
Like jewel orifice, mixing tubes are available in different sizes and life times. They are about 75 mm long with approximately 6 mm in external diameter. The external diameters range from 0.5 mm to 1.5 mm while 1 mm is most popular.
It is interesting to learn that mixing tube is replaced not because of wearing out, but more often, the brittle mixing tubes are damaged when nozzle accidentally gets in contact with work pieces or raised material on cutting table.
Alignment
It is critical to have precise alignment of jewel orifice and mixing tube especially when mixing tube size is relatively small. This is to ensure that the water jet passes directly down the center of the mixing tube. Otherwise the quality of the abrasivejet will be diffused, the quality of the cuts it produces will be poor, and the life of the mixing tube will be short.
The precise stainless steel holder is fit inside a bore with extremely high accuracy. The jewel orifice is mounted to the stainless steel holder. The mixing tube fits into a taper section in the jewel holder’s lower part. This design assures perfect alignment of the mixing tube and jewel holder
In the past, most nozzle designs required the operator to adjust the alignment of the jewel and mixing tube during operation. Modern nozzle designs rely on precisely machined components to align the jewel and mixing tube during assembly, thereby eliminating the need for operator adjustments.
Wearing
Jewel orifice, mixing tubes and Venturi chambers are three of consumables parts which are replaced regularly. The Venturi chamber is also subject to wear due to erosion acted on chamber side by abrasive stream entrained by the water jet. Some nozzles have built in carbide liner to minimize this wear. Some Ventrui chambers are mounted to jewel orifice to form a compact body. Every time when jewel orifice is replaced, Ventrui chamber is also replaced.
The nozzle body itself is not subject to abrasive flow and so its life time is so long.
It is also critical that soften water is required to maintain longest possible mixing tube life. If water contains too much minerals, scale deposit would be built up on the orifice jewel and thus, shortening life time of mixing tube and affecting jet quality as well.
Motion Equipment
Sturdy Floor Mounted Cantilever System with Precision X-Y Mechanism Driven by Steady Servo Motors
X-Y tables are the most common forms of motion system used in water jet cutting. This motion system consists of X-Y movement mechanisms and structures allowing cutting heads to move freely along both X and Y directions over work pieces.
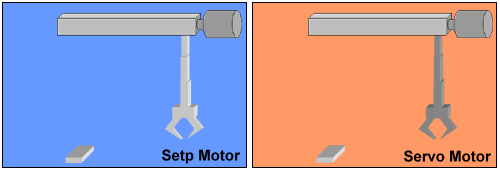
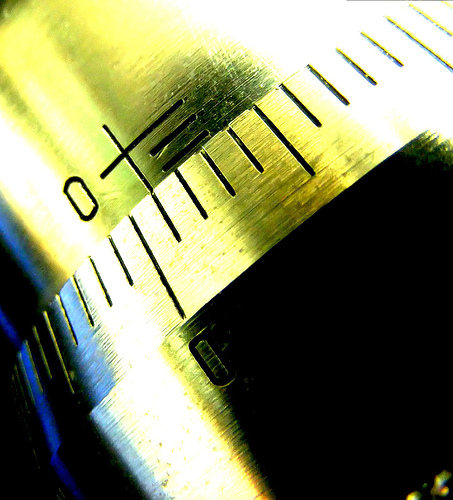
It employs a floor mounted X-axis and a cantilevered Y-axis mounted to the X-axis carriage. Cutting head is mounted to a carriage on the Y-axis.
The axis runs on specially treated high precision ball bearing linear screw and guide rail. Catcher tank and cutting table are totally separated from the X-Y motion structure.
The advantages of this independent cantilever design are,
- There is no external frame or rails of a gantry. Operators are easily access to the cutting table.
- Flexible free space is available for easy loading and unloading of work pieces. This gantry free designed is beneficial especially when work pieces are large and heavy.
- The cantilever beam moves at only one end. Eliminates the need for a precision dual-drive system required by a gantry beam.
Control System
Employ Popular dwg Files which are Converted to Numeric Files Automatically
Generally, it is a numerical control system with programs pre-installed. The designs are always done in an AutoCAD and are then stored in dwg files. These dwg files are then exported to the control system which automatically converts the dwg files into numeric files that the system can read. The machine then understands to where cutting head moves in X, Y and Z directions.
For advanced design, a servo system is employed. It controls servo motors which run in X and Y axis. The servo system assures higher cutting accuracy, faster speed, higher throughput and meanwhile, it is more reliable.
The most common logics, in terms of safety precaution, that could be achieved through the control system are,
- When filter is blocked, machine stops.
- When it is lack of water, machine stops.
- When pressure is too low, machine stops.
- When pressure is too high, machine stops.
Catcher Tank with Working Table
Feerly Movable Separate Catcher Tank Maximizes Fexibility of Large and Heavy Workpieces Loading
A catcher tank is used to collect water and abrasive during water jet cutting.
A working table is mounted on top of the tank. It is used to support workpieces on which they are loaded. The working table is generally a grating.
The catcher is separated from the floor mounted cantilever system. It allows easy access of operator. Flexible and more space make large and heavy workpieces loading easier and safer especially for those brittle materials such as glass.
Meanwhile, the separate table/tank can also be structurally simple and low in cost.
Abrasive Delivery System
Powerful System Feeding Accurate Amount of Abrasive Automatically
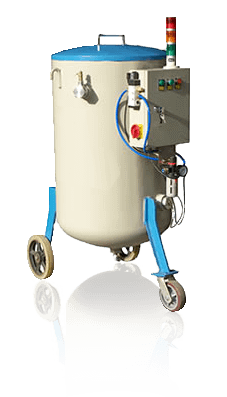
This system consists of a metering device where adequate amount of abrasive are scale. A simple fix ratio of abrasive flow to water flow is used for any kind of materials, with different thickness, to be cut.
The abrasive flow amount is measured during machine set-up and it is generally done once for all. The parameters will be stored in the control system and no further adjustment or fine tune of abrasive flow is required. These parameters, of course, could be changed anytime when necessary.
The only parameter required to adjust is nozzle traveling speed, which is the cutting speed. This is achieved from the numeric control system.