Features & Specs
Structure
Furnace
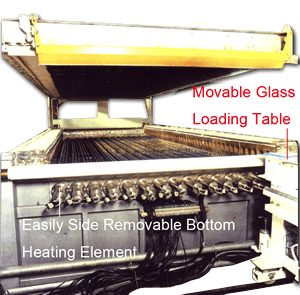
The frame is divided into two parts. The top part can be lifted by electromechanical jacks for servicing. The total insulation thickness is 250 mm consisting of several layers, the inner layer being of ceramic fiber for cleanliness. The ceramic rollers are furnished with self aligning bearing housings which are mounted to the outer structures far away from intense heat. The rollers are driven by an automatically controlled drive system through an electromechanical drive, a main drive shaft and toothed belts. This drive system and all furnace rollers run continuously on the same phase thus ensuring a high glass quality.
Heating System
The heating system consists of radiation heating elements similar to the conventional roller heart furnace. In order to give a very even heating and to enable a good heating of different glass types (normal float glass, coated glass, reflective glass, low E glass, etc.) an additional convection heating is included. The system is vital also for improved yields and capability to temper well glasses with holes, notches etc. Furthermore, the capacity increase is an added benefit.
The convection heating is arranged in such a way that the hot air is taken from the furnace and blown on the glass surface by small electrically driven hot resistant blowers via pipes and nozzles. Thus air circulation is internal and avoids blowing of cold air into the furnace.
The top and bottom surfaces of the glass have separate convection systems thus allowing both surfaces of the glass to be heated at equal rates. The system enables the production of glasses with very high flatness. The radiation heaters are longitudinally installed in the furnace being individually controllable to allow heating profiles to be set for different glass loads.
Quench Section
The quench section is featuring high efficiency quench nozzles, steel rollers with “KEVLAR” windings and high pressure blowers with motors controlled by inverter. The top and bottom nozzle blocks are installed and linked together by heavy duty roller chains driven by an electro-mechanical drive. The distance between the nozzles is automatically adjustable for different glass thickness according to the reading of the pulse counter. After tempering the quench heads move automatically away from the glass (up/down) to allow cleaning the chillers from broken glass.
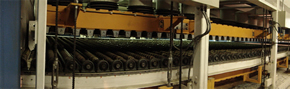
Blowers & Air Ducts
The blowers are high pressure centrifugal blowers suitable for variable loads as required for the glass tempering. Both the blower and the motor are installed on a heavy duty base. Flexible mounting supports are used so that the package can be installed on a normal factory floor.
The air ducting is designed for minimum pressure loss. Separate ducts and flexible bellows are provided for the top and bottom quench heads. A control flap allows to adjust the pressure between the top and bottom sections separately. Both sections have their own pressure gauges.
Loading & Unloading Tables
The tables are equipped with steel rollers made of high precision steel pipes with machined shaft ends mounted on self-aligning bearing blocks. The rollers of the loading table are covered with rubber hoses except the rollers situated in the hot area near to the furnace door. The rollers of the unloading table are covered with “KEVLAR” windings. The roller tables are driven by an electromechanical drive, sprockets and a roller chain. The control is computerized with the exception of the step drive needed for easy loading and unloading of the whole loading area.
Control System & Electrical Cabinet
The operation is highly automatic for an easy operation and a high glass quality. After settings the furnace functions are automatic. All settings are done from the main control panel. The system is constructed of commercially available components for a high reliability, good service and easy availability of spares.
The control system consists of a PLC control unit assisted by an industrial personal computer with Windows based software. Most functions and controls are shown on a high resolution 14” colour monitor display and are controlled by an industrial type keyboard or switches.
The control system includes alarms for possible malfunctions with indication of the location and type of the malfunction. Emergency stop push buttons and functions are included for special circumstances. The electric switchboard includes main switches, relays and all necessary components installed in steel cabinets.
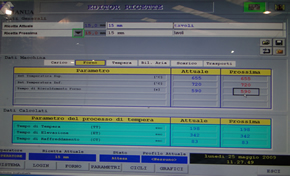